Product brief description
No. |
Items |
Spec: |
1 |
Material |
Thickness:0.8-3.5mm(according to the customer requirement)
Input width:75~285mm(according to the customer requirement)
Inner Diameter of Coils:508mm
Outer Diameter of Coils:Φ1100~Φ1600mm
material: carbon steel ,Low carbon steel
|
2 |
Power supply |
6. 380V three-phase electricity 50Hz(according to the customer requirement) |
3 |
Capacity of power |
main power:About 600KW |
4 |
speed |
90m /min |
5 |
Total weight |
Approx.20 tons |
6 |
Dimension |
Approx.(L*W*H)for roll forming machine:Approx 23m*2m ( according to the using) |
7 |
Cut style |
Fly sawing cutting |
Product details description
Speed:90m /min
Total weight:Approx.20 tons
Capacity of power:main power:About 600KW
Hydraulic Uncoiler ( Double head) :
Shearing & Welding Machine
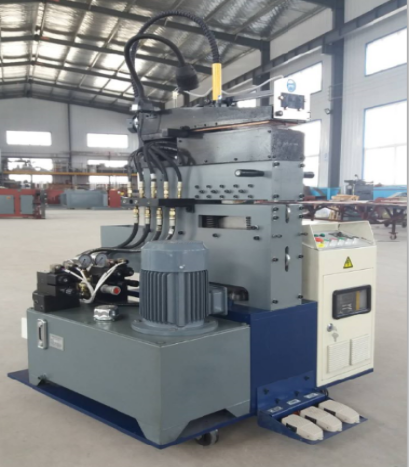
Horizontal Accumulator
Forming & Sizing Mill:
Scarfing roll stand:
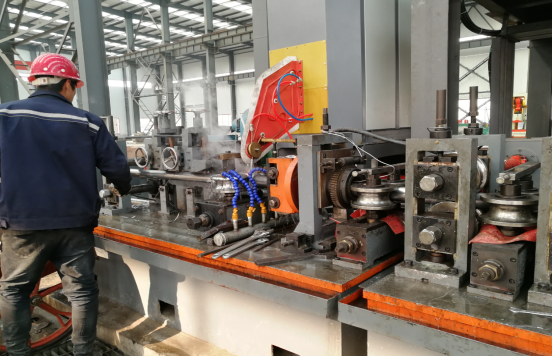
Flying cutting saw
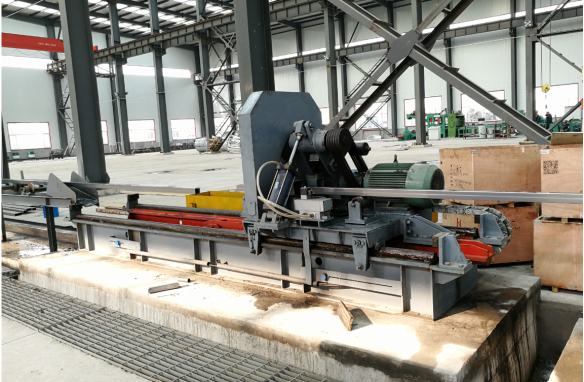
Product parameters table
1 Hydraulic Uncoiler ( Double head)
The uncoiler is designed to support the steel coil and provide production
material for the whole tube mill line.
Width of strip |
75-240mm |
Weight of strip |
single coil Max.3 tons, double head total max 6 tons |
Expansion Type |
Hydraulic Expansion |
Brake |
Pneumatic brake |
Work head turning |
Manual turning |
Width of strip |
75-285mm |
Strip thickness |
0.8~3.5mm |
Cutting Type |
Hydraulic Shearing |
Welding Method |
Argon arc Welding |
Argon Gas |
Purity more than 99.99% |
Steel Grade |
σb≤520 MPa σs≤235Mpa |
2 Shearing & Welding Machine
Shearing & Welding Machine is used to cut the irregular ends of the
strips and then connect the two strip ends by argon arc welding, with pneumatic
shearing and automatic welding, working time of 2-3 minutes.
Width of strip |
75-285mm |
Strip thickness |
0.8~3.5mm |
Cutting Type |
Hydraulic Shearing |
Welding Method |
Argon arc Welding |
Argon Gas |
Purity more than 99.99% |
Steel Grade |
σb≤520 MPa σs≤235Mpa |
3 Horizontal Accumulator
To guarantee continuous production, the Accumulator stores strip allowing
time for the operator to use the shear and end welder to connect the strips. The
device is convenient in installation and easy to operated.
Strip width |
75~240mm |
Strip thickness |
1.2~3.5mm |
StoringCapacity |
0m –300m |
Feeding speed |
Max 120m /min |
Feeding Motor |
18.5kW |
4 Forming & Sizing Mill
Forming & Sizing Mill, forms the steel strip of a certain specification
into tube blank and welds them into rounds with HF current. When the gradually
rolling strip starting from the edge guide to the weld box reaches the HF
welder, the W roll forming mode and induction welding adopted in this mill line
is a proven designs. The two side of the strip are heated to the welding point
and are squeezed together.
Next are removing weld beads, cooling, sizing and roughly straightening.
The horizontal bottom line method is adopted in this mill and double radius
for the rollers.
This section includes the forming mill, welding machine, cooling device and
sizing mill.
Ø Main technical parameters:
Round pipe diameter: Φ 25~Φ90mm
Thickness round pipe : 0.8mm~3.5mm
Square pipe: 20* 20mm~70*70mm
Max. Working Speed: 90m/min
Master motor power: DC185KW
Forming method: Bottom line and “W” forming
Ø Mill stands lay-out:
H stands for Horizontal Stand, V stands for Vertical Stand, T stands for Turk
Head
General layout:Forming 7H8V, sizing 6H6V2T
Feeding---H1---H2---V1---H3---V2---H4---V3---V4---V5---H5---V6---H6---V7---H7---V8--
Guiding --- Squeezing-- Outer de-burring --- Polishing --- Water cooling
---V9---
H8---V10---H9---V11---H10---V12---H11---V13---H12---V14---H13---T1---T2
Ø Forming Mill Parameters
Feeding and leveling device: One set
Horizontal roll stand:
Horizontal roll axle diameter of 80mm, material of 40Cr, whole roll thermal
refining processed, surface high-frequency hardening processed.
Roll stands material cast steel or plate welded, gear slider block of 45
forged steel;
Side off when changing the rollers;
Vertical roll stand:
Vertical roll axle diameter of 50mm, material of 40Cr, whole roll thermal
refining processed, surface HF quenching processed;
Vertical roll base material cast steel or plate welded;
Gear Distribution box:( with Universal Shaft)
Box body: plate welded
Gear material: 20CrMnTi, carburizing and quenching
Seam guide stand:
The roll stand can be adjusted in several directions so that the seam can be
guided into the welding position correctly.
2 roll Weld box( 2 Rolls ) with scarf bead :
This section is used to squeeze the two HF heated edges forging them
together. It has 2 rolls to make the two halves to be properly contoured during
the forging of the two heated edges.
Side Roll axle diameter Φ55mm;Roll shaft material 40Cr;
Scarfing roll stand:
Two scarfing stands to remove the external weld bead; the scarfing tool can
be adjusted horizontally and vertically. crosswise and longitudinally, and with
quick lift function and two holding rolls.
Polishing roll stand:Free drive stand
polish the welding seam after scarfing;
Structure: two passive roll, gantry structure
Roll axle diameter: 80mm, material of 40Cr
Water cooling section:Length ( 2m)
Spraying and submersion at the same time to quickly make the tube cool and
prevent the tube from shaping when sizing.
Sizing Mill
Horizontal Roll Stand:(Refer to that in the forming mill)
Vertical roll Stand:(Refer to that in the forming mill)
Turks Head Stands: 2 sets
Four rolls on each head (stand) can be adjusted in several directions to
straighten the tube
reversely and then deliver a straight tube properly shaped the pipe into the
cutting section straightly.
Roll axle diameter: 50mm, material of 40Cr;
Gear distribution box:(Refer to that in the forming mill)
Master drive system:
DC185KW, with hard face reducer;
All the mill worktables
Transmission shafts one set;
Water piping inside the tube mill
5. Flying cutting saw
Flying cutting saw is used to precisely cut the pipe to length automatically
under the condition that the pipe continuously delivered from the mill at high
speed.
Diameter of pipe |
Φ25mm~90mm |
WT of pipe |
0.8-3.5mm |
Fixed Cutting length |
6m |
Cutting Accuracy |
0-6mm |
Saw cutting motor |
30 KW |
Carriage driving motor |
22 KW |
Saw blade size |
600mm |
Cutting Speed |
Max.90m/min |
6. Solid-state High Frequency Welder: 300 KW
Solid state H.F. welder main circuit structure is a typical AC-DC-AC variable
frequency structure. Rectifier adopts 3-phase bridge style thyristor
phase-control rectifier circuit, DC side adopts inductor, capacitor to compose
LC filter which meet the working requirements of voltage type inverter. The
voltage type inverter adopts modularization parallel structure to extend power
supply power, each inverter module is single phase MOSFET bridge style circuit
connected with series resonance tank circuit by H.F. matching transformer. On
one hand, the matching transformer realizes power combination and impedance
matching; on the other hand it realizes electric isolation of load and power
supply. To put effective and swift protection on over-current malfunction of
voltage type inverter, our company introduces special and stable over-current
protection circuit which guarantees safe and stable running of inverter.
Welder include:
Switch rectifier cabinet, inverter output cabinet, water to water cooling
system, central control table, mechanical adjustment device and so on.
DC drive system: Euro 590 speed controller
Forming and sizing mill motor control: Euro control device;
7 Run-out Table
The finished pipes run along the roll table and goes to the bench. Then
simple packing machine collects the pipes into needed shape.
Motor of roll bench: 3Kw , speed adjustable;
8 Tooling:
Material Cr12, hardness HRC58-62; squeezing roll material H13;
Tooling size: 25mm,40mm,90mm