Sandwich Panel Production Line
PU sandwich panel production line is an automatic production line which included many kinds of technologies such as machinery, chemical engineering, electronic control, hydraulic press, air-operated and temperature control. The whole line is consist of decoiler system, coating and cutting system, rolling system, preheat system, foaming system, the double track system, cutting system, cool system, air-operated system and so on.
PU sandwich panel use the hard anti-burning polyurethane foaming plastic as the core material and the color-coated sheet as the plane material, and formed through rolling. Cause the light, high strength, adiabatic, waterproof, decorative performance, the PU sandwich are used as roofing and wall sheets for factories, warehouses, gyms, residential houses, villas, portable, combined refrigeratiory, etc.
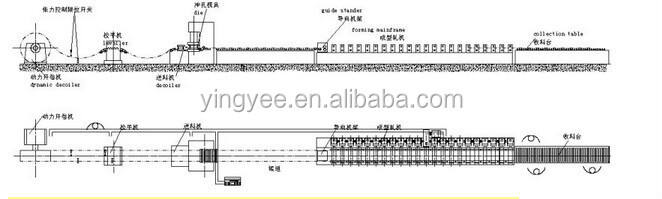
Product Description
Main Components
PU sandwich panel machine mainly consists of hydraulic uncoiler, film covering system, roll forming
machine, polyurethane foaming system, double belt system, automatic cutting device, electric control system, hydraulic system, and pneumatic system. Stacking system and packing system for option.
Technical specification
Sandwich Panel Spec |
Min. cutting length |
3 meters |
Max. stacking length |
15m |
Panel width |
1000mm |
Panel thickness |
Mini
thickness
|
40mm (corrugated sandwich panel) 50mm (wall panel) |
Max.
thickness
|
150mm
(exclude corrugated sandwich panel)
|
Steel Sheet Spec |
Thickness |
0.4-0.7mm color steel sheet |
Width |
1250mm |
Max. coil weight |
10 tons |
Inner Dia. of coil |
508mm, 620mm |
Whole Line Spec |
Working speed |
About 3-7m/min (adjustable) |
Total length |
about 90m |
Working height |
1200mm (height of panel coming out) |
Pressure for foaming |
150-200 bar |
Double belt conveyor |
23m |
Control mode |
Mitsubishi PLC and converter |
Total power |
About 100Kw (as per final designing) |
Power required |
380V/3phase/50Hz |
Air pressure |
0.7Mpa (for buyer to prepar |
Features:
1. Beautiful appearance, low noise, high efficiency.
2. Multiple function: could produce 4 kinds of panel ,wall pane ,roof panel ,cold room panel ,and garage door panel.
3. The line employs advanced PLC and sets the panel length and cuts the panel automatically.
4. The main body is welded with type "H" section steel as its material,strong strength.
5. The roll forming machine is adjustable ,the suitable width range is 600-1250mm.
6. The roller matrial is medium carbon alloy steel ,with high quality.
7. The length of double belt laminating machine could be made according to customers needs.
Pictures of machine:
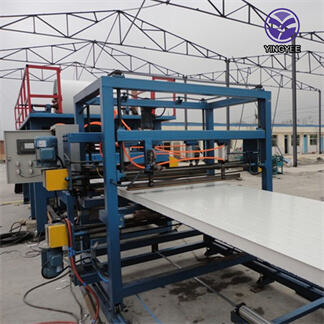
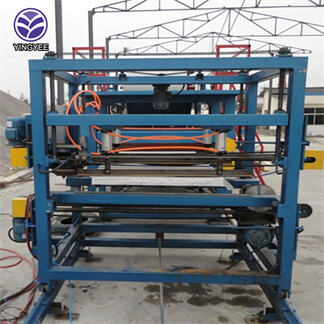
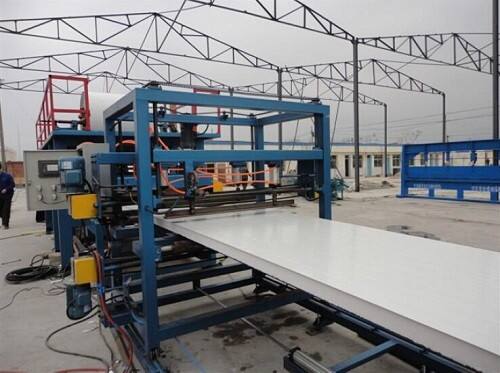
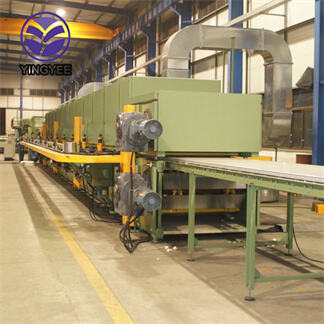
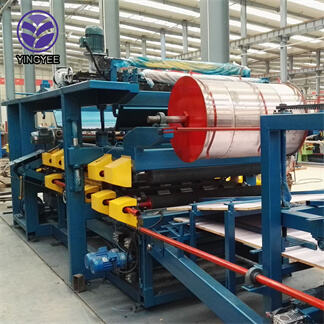
Packaging & Shipping
Main machine is nude, the computer box is packed by plastic film.
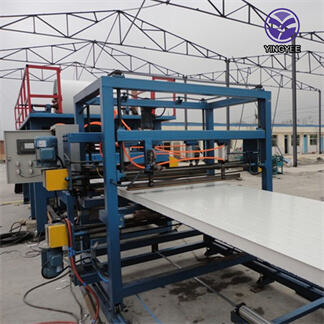
Company Information
Shijiazhuang Yingyee Import&Export Co., Ltd.
YINGYEE is the manufacturer specialized in various cold forming machineries and automatic production lines. We have a wonderful team with highly technology and excellent sales, which offer professional products and related service. We paid attention to quantity and after service, got great feedback and honor fromall the clients. We have a great team for after service. We have sent several patch after service team to oversea to finish the products installation and adjustment.
Our products were sold to more than 20 countries already. Also included US and Germany.
Main product :
Roof roll forming machine
Roller shutter door roll forming machine
C and Z purlin roll forming machine
Downpipe roll forming machine
Light keel roll forming machine
Shearing machine
Hydraulic decoiler
Bending machine
Slitting machine
FAQ
Training and Installation :
1 We offer installation service local in paid, reasonable charge.
2 QT test is welcome and professional.
3. manual and using guide is optional if no visiting and no installation.
Certification and after service:
1. Match the technology standard, ISO producing certification
2. CE certification
3. 12 months warranty since the delivery. Board.
Our advantage:
1. Short delivery period.
2. Effective communication
3. Interface customized.
Introducing, the all-new Automatic Rock Wool/EPS Sandwich Panel Roll Forming Machine/Roof Tile Production Line by YINGYEE, the leading manufacturer of roll forming machines. This cutting-edge production line was designed to meet the high demands of the construction industry, with seamless and efficient production of high-quality rock wool/EPS sandwich panels and roof tiles.
It features an advanced technology that ensures precise and consistent panel for tile specifications. The manufacturing process is completely automated and computer-controlled, reducing the danger of human error and providing constant quality output.
This is versatile and can create a wide range of rock wool/EPS sandwich panels and roof tiles with varying thicknesses, dimensions and profiles. The production line includes a decoiler, which feeds the material in to the machine is roll-forming. The roll-forming machine then forms the material in line with the desired profile, with a high persistence and precision. Next, a very efficient cutting system will cut the panels or tiles precisely to the required length.
It operates at high speed, delivering a manufacturing rate of up to 12 meters per minute, which makes it one of the forming machines available in the marketplace. This high coupled output comes with a low manufacturing costs makes this device very lucrative for commercial use.
This item is user-friendly. Even individuals with no prior experience in roll forming can certainly operate this machine with just minimal training.
It was made tto be highly reliable and durable, constructed with top-notch steel and supported by robust framework that improves its structural strength. The machine was designed with safety features that help to cut back accidents and guarantees operator safety.
Choose YINGYEE for reliable and durable roll forming machines that guarantee productivity and profitability. Order your YINGYEE’s Automatic Rock Wool/EPS Sandwich Panel Roll Forming Machine/Roof Tile Production Line today.