Product brief description
No. |
Items |
Spec |
1 |
Cabinet |
1. Thickness: Max 0.8mm
2. Depth: 200/300mm
3. Width:250-400mm, height:300-600mm
4. Material:GI coils
|
2 |
Power supply |
380V, 50Hz, 3phase |
3 |
Capacity of power |
Main power:7.5KW |
4 |
Total weight |
Approx. About 9Tons |
5 |
Dimension |
Approx.(L*W*H) About23×3×2m |
6 |
Stands of rollers |
About 14 steps roller |
7 |
Cut style |
Automatic folding and cutting system |
Product details description
1.Decoiler support steel coil for uncoiling.
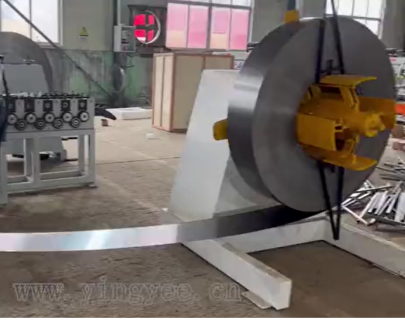
2. The steel coil passes through the leveling machine.It makes the steel coil
flatter.
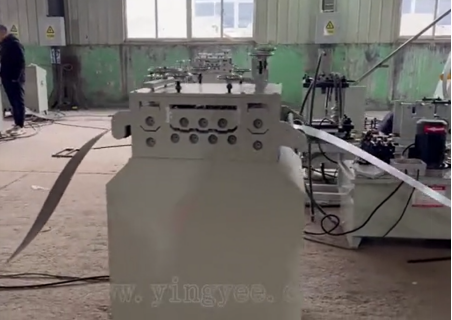
3. The flat steel coil enters(servo feeding) the punching device.It can
complete the production of the four corner holes of the box, Air vent, and hinge
holes.
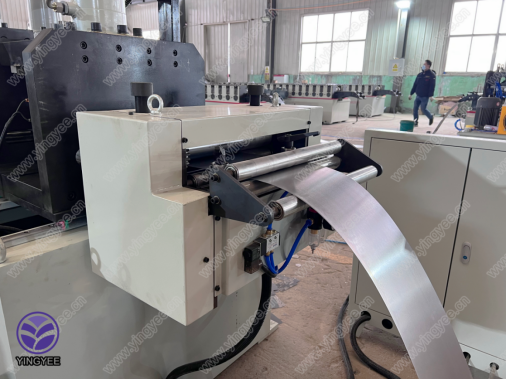
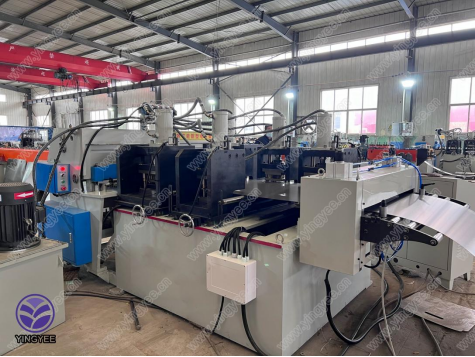
4. In the forming part, The steel coil is gradually folded and shaped
according to the designed drawings.

5. The bending device bends the product to form a frame.The bending device
bends the product to form a frame. It is bent 3 times for cutting.
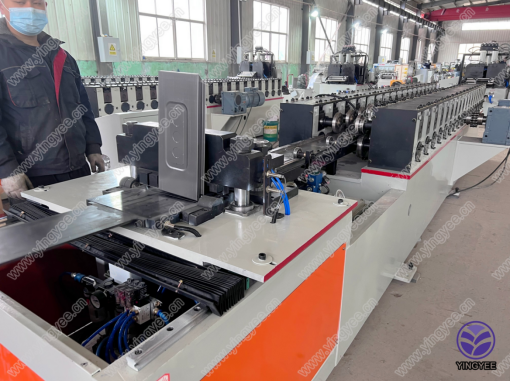
Product parameters table
3 tonsmanual decoiler |
Inner diameter ofsteel coil: φ500mm; material thicknessis max 0.8mm
Carrying weight: ≤3T
Spindle center height: 650mm
Support form:Inner tension
|
Traction and Leveling machine |
Roller traction leveling
Leveling thickness: Max 0.8mm
Power: 2.2kw |
NCF-400 Servo Feeder |
Servofeedingcontrol,Multi-stage feeding
Servo motor: INVT
Feeding accuracy:± 0.1mm/time |
Punching system |
Composed of a 5-cylinder hydraulicpunching machine;
No.1punching machine:Complete tapping and stretching threading holes (incremental type)
No.2Punchingmachine: Completethe front blinds
No.3Punchingmachine: Complete theback blinds
No.4 cantileverpunching machine:Complete double front corner cutting and hinge of the box body
No. 5 cantileverpunching machine: Complete double rear corner cutting of the box body
(The 5th cantileverpunching machine is located opposite the 4th cantileverpunching machine) |
Punching moulds |
1 set knock holes mold
2 sets molds for front and back blinds
1 set front corner cutting and hinge combination mold
1 set rear corner cutting combination mold
Mold material: SKD11
|
Roll forming machine |
Cantilever roll forming machine:Rapid depth adjustment
Including door depth: 200/250/300mm
Material thickness: Max 0.8mm
Front waterstop size: 20mm
Formingsteps: About 14steps
Forming machine shaft:45mm
The roller is forged with Cr12 and CNC processed after overall quenching, with a hardness of up to HRC58-62° |
Automatic folding and cutting system |
Form: The combination of gas and liquid combination
Minimum 300 * 250
Maximum1000 * 1200
Cutting/folding: Combination integrated
Blade material: SKD11
Folding: Automatic folding
Power: 3KW |
Electrical control system |
Mitsubishi PLC,
Human machine interface, enabling interaction between humans and PLC |